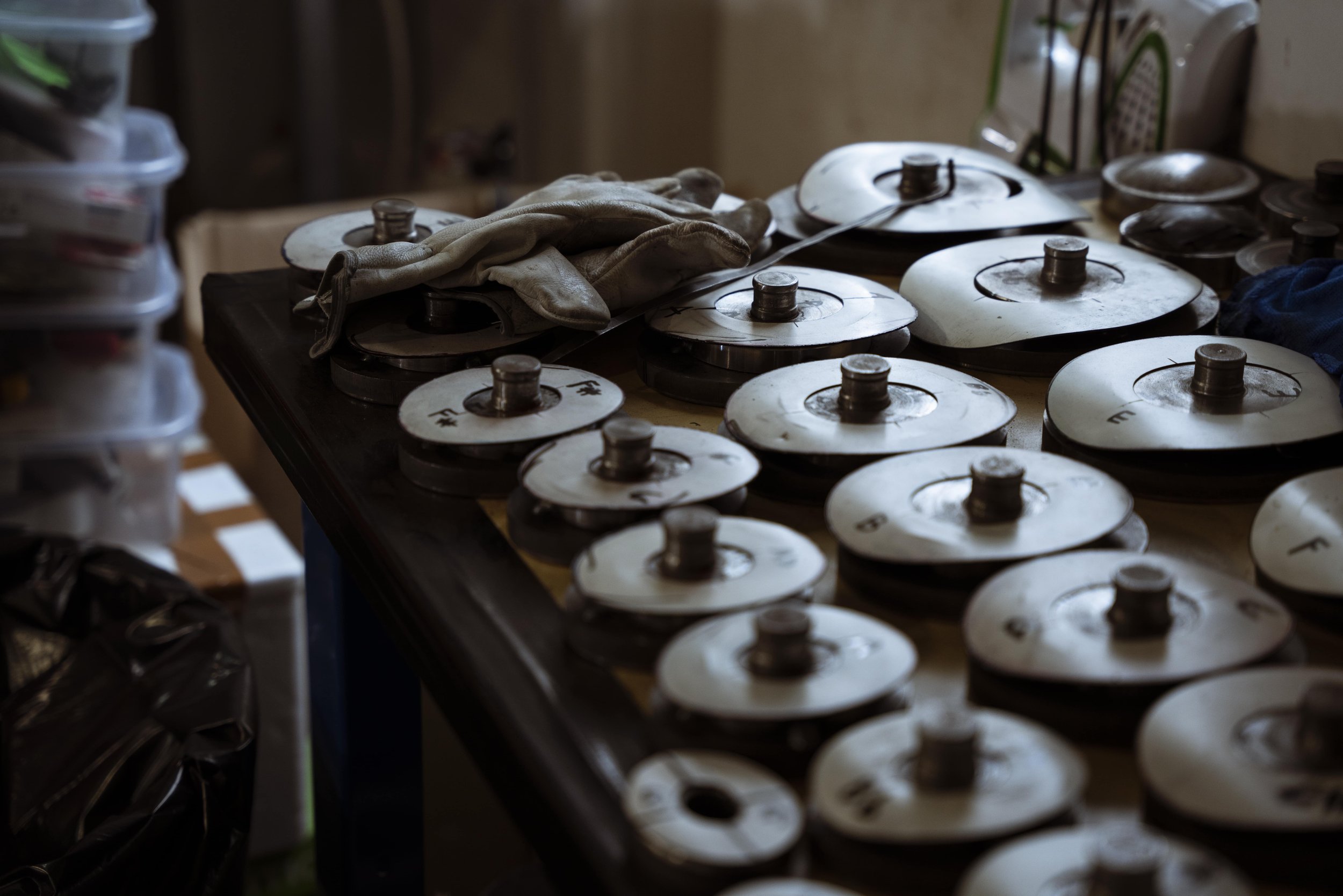
Hand-pan.
A pan that you play with your hands.
Literally.
A Handpan is really all about how you make it. So, let me tell you how I do it.
For Nerds Only
A Handpan is a percussion instrument that was invented in 2000. It’s composed of two connected half-shells, made of dc04 iron. At the top center you find the Ding, surrounded by (at least 7) tone-fields that produce different sounds when touched. At the bottom you can find a opening, called Gu.
I start from the dc04, inox or ember steel sheets, which I shape into circles, usually with diameters between 50 and 60 cm, and then into the concave and convex halves.
Tones are printed on the sheets with a hammer and a mallet. It’s a process that can require me up to 5 days (and more than 40k hammer strokes by hand), and it’s crucial for the instrument to play gracefully and with a stable tuning.
Afterwards, I mold the edges are into a more rounded and comfortable shape for the fingers, which also improves the transmission of sound waves.
Each half-shell goes through Nitriding: I immerse them in special tanks, in a bath of salts at high temperatures, to make them stronger and more resistant to oxidation.
Assembly is the following step, after which the tuning thakes place, by making use of hammers and other specific tools. Precision is quintessential in this phase, to guarantee harmonic sounds.
Lastly, I refine the handpan and levigate it. The surface is polished and I apply protective finish, to prevent corrosion and impove the aesthetics.
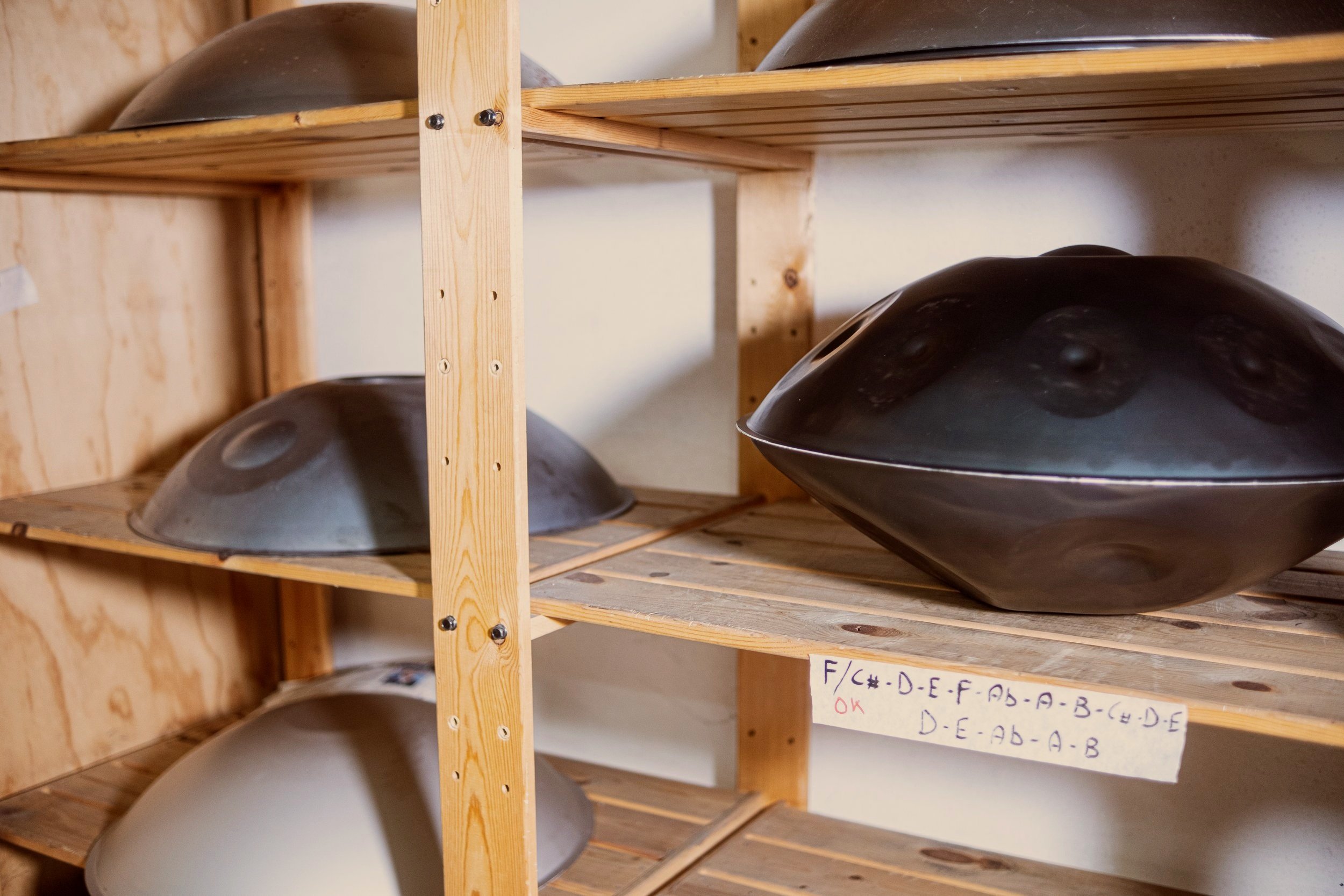